Its all about sulphur
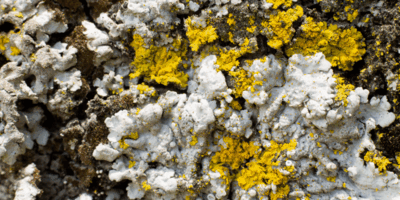

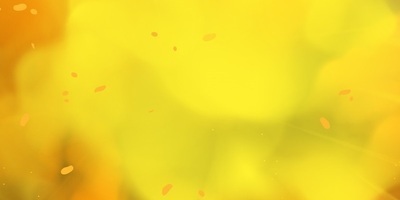
• Claus Technology
• Oxygen Enrichment
• Tail Gas Treating Process
• Iron Sponge Process
• FGD Process
• Liquid Redox Process
DESULF ALSO SUPPLIES CHEMICALS
Crude oil and natural gases that are naturally available from underground invariably contain sulphur in the form of poly-sulphides. The sulphur content in crude oils varies from less than 0.05 to 5.00 % by weight. Oils containing less than 1% by weight of sulphur are generally categorised as sweet and with that of higher than 1% by weight are generally considered as sour. Natural Gas ,also,may contain up to 28% by weight of sulphur compounds. Natural gas may also contain carbon-di-oxide. Both sulphur and carbon di oxide is required to be removed to levels of 4- 10 ppm to make the natural gas sweet. Crude Oils by itself has limited applications. It needs to be processed in oil refineries value added products like motor spirit (MS), diesel, fuel oils and gas etc. MS, diesel and fuel gas find maximum applications in the transportation sector. Sulphur, if not removed from crude, crude products, fuel oils and gases releases Sox to the atmosphere which significantly contributes to pollution. It is a greenhouse gas and contributes towards to global warming. It causes acid rain which destroys plants, agriculture and foliage. It also adversely human health. Since the advent of and gas processing technologies towards the early and middle parts of the last century, the emphasis was more on production of crude derivatives and low emphasis was given to reduction of pollutants like NOx and SOX CO2 CO etc. Towards the end of the last century, environment emission standards came into force and refineries were forced to adopt technologies for reduction of SOX, NOX and other pollutants. This created an opportunity to extract sulphur from crude and gas derivates. It was a WIN-WIN situation as refiners got an additional product to supply through sulphur extraction process and at the same time it helped reduce pollution. International Maritime Organization (IMO), on 1st Jan 2020, introduced new regulations mandating the use of max 0.50% sulphur in fuel oils to be used for the marine industry. This has sent ripples around the world.
More such regulations are under way in other areas as well.
Sulphur is an extremely useful element. Its largest application is for the manufacturing of fertilizers with other principal uses including rubber industries, sulphuric acid manufacturing industries, pharmaceutical industries, cosmetic industries etc. Sulphur is present in many raw industrial gases and in natural gas in the form of H2S. The toxic H2S fumes that characterize many gas processing, refinery operations and petroleum production sites represent a genuine threat to our environment. Concentration level of H2S varies significantly depending upon their source. H2S produced from absorption processes such as amine treating of natural gas or refinery off gases can contain 50-75% H2S by volume or higher. Many other processes can produce H2S with only ppm concentration but in quantities which preclude the gases from being vented without treatment.
The large variation in concentration and flow requires different methods of H2S removal. For relatively small quantities of H2S, scavenger processes are used. For Sulphur production up to approximately five tons per day, liquid reduction– oxidation (REDOX) processes are common. The Claus process is the most widely used process for conversion of H2S to elementary Sulphur.
WE OFFER THE FOLLOWING TECHNOLOGY
CLAUS TECHNOLOGY
Feed gas in a Claus sulphur recovery unit usually originates from acid gas sweetening units.The stream containing, varying amount of H2S and CO2 is saturated with water and frequently has small amounts of hydrocarbons and other impurities in addition to the principal components. In a typical Sulphur recovery unit, H2S (concentration: >50% by volume) bearing gases enter at about 0.7-0.8 Kg/cm2g Click here to know more
OXYGEN ENRICHMENT
Since air consists of approximately 79% nitrogen and 21% oxygen, the introduction of air to supply oxygen for combustion of H2S to SO2 also introduces a large quantity of nitrogen. When air is used as oxygen source, approximately 5.6 moles of nitrogen are introduced into the gas flow for every mole of H2S that is burned. Nitrogen does not react, and the added mass of nitrogen lowers the adiabatic flame temperature in the reaction furnace. The nitrogen must also be heated, cooled and reheated through combustion, Sulphur condenser and reheater ahead of rectors.Click here to know more
TAIL GAS TREATMENT
Conventional Claus Sulphur Recovery Units are limited because of equilibrium limitation and a three stages or four stages sulfur recovery unit cannot meet the minimum environmental pollution agency sulphur recovery levels. This involves a tail gas treating unit at downstream of sulfur recovery unit. Click here to know more
FGD TECHNOLOGY
FGD Process reduces emission of SO2 from various refinery flue gas streams, Sulphur plants and spent acid regeneration units. The process uses an aqueous amine solution to achieve highly efficient, selective absorption of SO2 from flue gas. Click here to know more
IRON SPONGE PROCESS
Iron Sponge Process is based on the reaction of hydrogen sulfide with iron oxide in which the gas is passed through a bed of wood chips impregnated with iron oxide. The process scavenges hydrogen sulfide and organic sulphur compounds (mercaptans) from gas streams through reactions with the solid-based chemical adsorbent. Click here to know more
LIQUID REDOX PROCESS
Liquid redox is used to remove hydrogen sulphide (H2S) from sour natural gas and other gas streams by converting it to solid elemental Sulphur for sale or disposal. It is based on a reduction-oxidation reaction carried out in an aqueous solution and catalysed by iron which is held in solution by organic chelating agents.Click here to know more
OUR SERVICES
- Selection of most appropriate process
- Preparation of Basic design and Engineering Package for Grassroots Sulphur Recovery Unit, Tail Gas Treating Unit, Biogas Sweetening Unit, Flue Gas Desulfurization Unit
- Revamp of Claus based Sulphur recovery unit for capacity enhancement
- Revamp of Claus based Sulphur recovery unit for Sulphur recovery improvement
- Technical service assistant for trouble free operation and performance improvement of Sulphur recovery unit, tail gas treating units and all other gas sweetening units for natural gas and biogas purification
- Assistance in pre-commissioning and commissioning activities
SUPPLY OF CHEMICALS
We also supply sulphur and non sulphur chemicals required for industrial plants Click here to know more