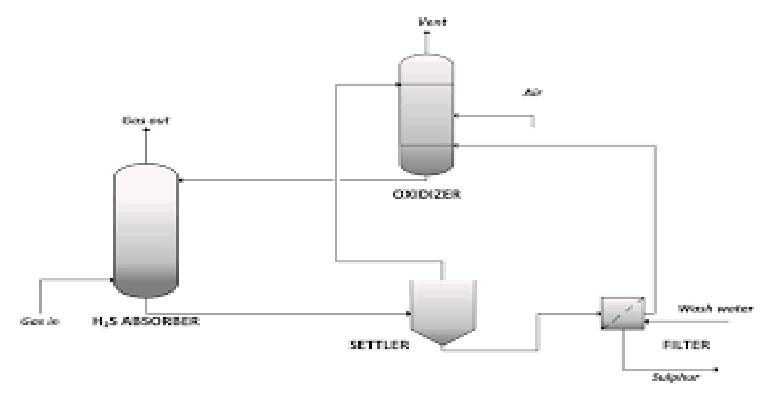
LIQUID REDOX PROCESS
Liquid redox is used to remove hydrogen sulfide (H2S) from sour natural gas and other gas streams by converting it to solid elemental sulphur for sale or disposal. It is based on a reduction-oxidation reaction carried out in an aqueous solution and catalysed by iron which is held in solution by organic chelating agents.H2S contacts the liquid redox solution inside the absorber and is converted to elemental sulphur and water. The exothermic absorber reaction represents the oxidation of H2S to elemental sulphur and the accompanying reduction of the ferric iron state (active) to the ferrous iron state (inactive). All reactions take place in solution at near ambient temperature, making the process inherently safe. The working solution operates at a pH between 8 and 9. NaOH or KOH is used to control the pH.
The solution is then routed to the oxidiser where the catalyst is regenerated using air. The oxidiser reaction in the regenerator (also exothermic) represents the oxidation of the ferrous iron back to the ferric iron state. Regenerated solution is pumped back to the absorber. Removal of sulphur from the unit is accomplished by directing a slip stream of circulating solution to a sulfur filter system. The sulfur filter may be configured in several ways, but the objective is always the same: recover as much chelated iron solution as possible while concentrating the sulfur into a solid cake. Not all of the solution is recovered. Some catalyst, chemicals and salts formed in side-reactions (e.g. sulfates, thiosulfates, carbonates and bicarbonates), and some products of chemical degradation will be lost in the sulphur cake. As solution is lost, some catalyst is also lost, which will be replaced with fresh catalyst addition. Liquid redox process can treat virtually any kind of gas stream and, as a result, the technology has been applied in a wide variety of applications to achieve 99.9%+ H2S removal in a single stage
The process is commonly used when the gas stream has a low content of hydrogen sulfide, thus Claus technology is not feasible. This process is useful also when low gas flow rates result in a non-economic application of direct oxidation processes such as Claus .The process can also be used as a tail gas treating unit (TGTU) or integrated into a TGTU downstream of a Claus SRU.